Protokół szczelności gazowej: Przewodnik 2025
Kto by pomyślał, że kawałek metalowej rury może wzbudzić tyle emocji, zwłaszcza gdy mówimy o bezpieczeństwie! A jednak, instalacja gazowa w naszych domach czy biurach wymaga bezwzględnej uwagi, czego nieodzownym elementem jest Protokół z przeprowadzonej próby szczelności instalacji gazowej w obiekcie. Ten z pozoru nudny dokument to nic innego jak świadectwo, że nasz system dystrybucji gazu jest bezpieczny i sprawny. To właśnie ten protokół dokumentuje formalnie pomyślny wynik badania, eliminującego ryzyko ulatniania się gazu, co jest kluczowe dla uniknięcia poważnych zagrożeń. Bezpieczeństwo przede wszystkim, zgadza się?
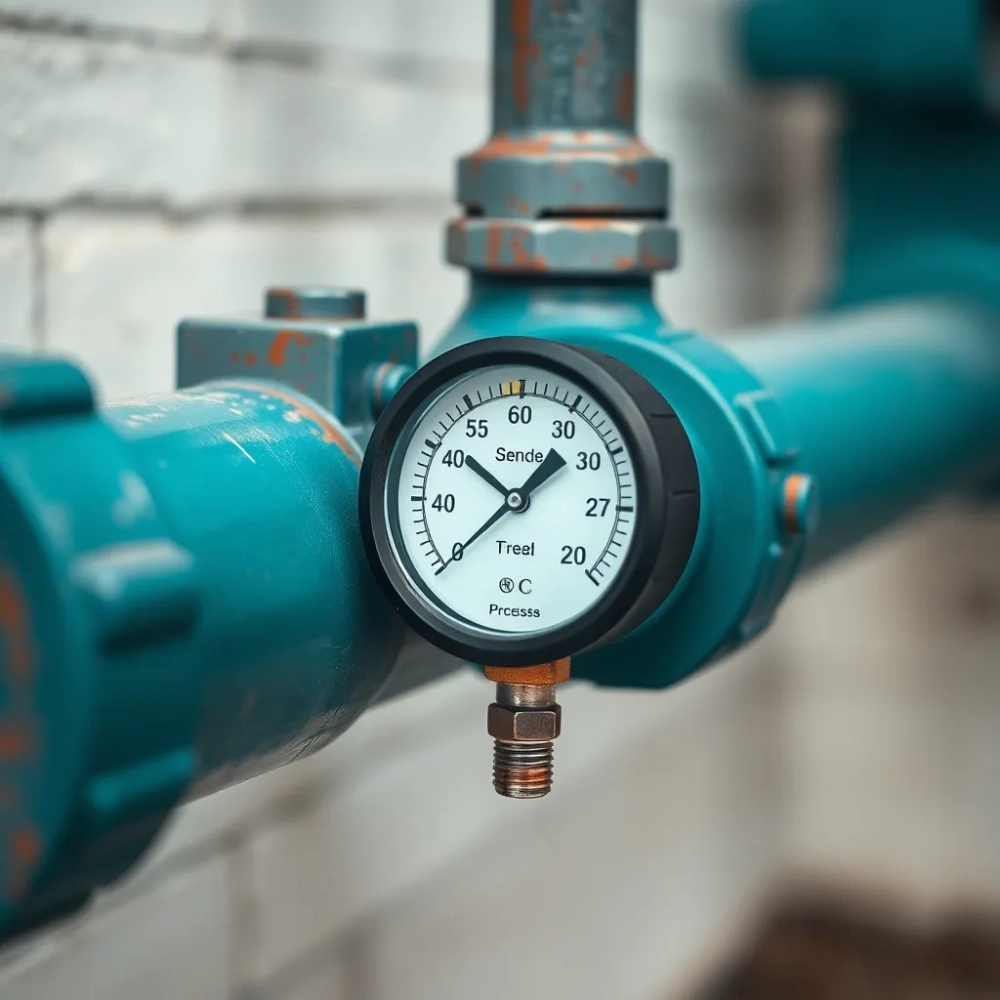
Próba szczelności instalacji gazowej to nie kaprys, a ścisła procedura, która weryfikuje, czy żaden milimetr sześcienny gazu nie ucieka tam, gdzie nie powinien. Myślimy o niej rzadko, dopóki wszystko działa poprawnie. Jednak jej przeprowadzenie, zwieńczone rzeczonym protokołem, jest wymogiem prawa i zdrowego rozsądku. Czy to nowo położone rury w kuchni, czy rozbudowa systemu grzewczego w całym budynku – test szczelności jest obowiązkowy. To tak, jakby sprawdzać hamulce w samochodzie przed każdą dłuższą podróżą. Niby oczywiste, a jednak wymaga konkretnych kroków i dokumentacji.
Kryterium Badania Szczelności | Procent Obiektów Pozytywny Wynik | Typowe Problemy |
---|---|---|
Pierwsza próba po montażu | 85% | Nieszczelne połączenia gwintowane, uszkodzone uszczelki |
Próba po remoncie/przebudowie | 92% | Uszkodzenia mechaniczne rur, nieprawidłowe połączenia spawane/zaprasowywane |
Próba po długim okresie wyłączenia | 98% | Korozja, osłabione uszczelki w zaworach |
Analizując dane dotyczące prób szczelności, widzimy wyraźnie, że najczęściej problemy pojawiają się zaraz po zainstalowaniu nowego systemu. To naturalne, ludzka ręka bywa omylna, a proces montażu jest złożony. Remonty i przebudowy też niosą ze sobą ryzyko, choć mniejsze. Największa skuteczność testów widać w przypadku ponownego uruchamiania instalacji po przerwie – jeśli przetrwała nieużywana, szansa na szczelność jest bardzo wysoka. Jednak nawet w tych "dobrych" scenariuszach, niewielki procent obiektów wymaga poprawek. To pokazuje, jak ważny jest ten proces weryfikacji.
Kiedy wymagana jest próba szczelności instalacji gazowej?
Każdy kto miał do czynienia z instalacjami gazowymi, czy to jako właściciel domu, inwestor, czy wykonawca, wie, że bezpieczeństwo nie jest kwestią do negocjacji. Przepisy prawa budowlanego, a konkretnie rozporządzenie w sprawie warunków technicznych jakim powinny odpowiadać budynki i ich usytuowanie, jasno określają momenty, w których próba szczelności instalacji gazowej jest nie tylko zalecana, ale bezwzględnie wymagana. Ignorowanie tych przepisów to nie tylko ryzyko kary finansowej, ale przede wszystkim narażenie życia i zdrowia użytkowników obiektu. To nie jest coś, co można odłożyć na później, albo, jak to mówią, "załatwić po znajomości".
Jednym z kluczowych momentów, kiedy pojawia się konieczność przeprowadzenia próby szczelności, jest wykonanie nowej instalacji gazowej. Kiedy nowy system rur i połączeń zostaje zamontowany, od piwnicy aż po punkt poboru gazu w kuchni czy kotłowni, bez testu szczelności nie ma mowy o dopuszczeniu go do eksploatacji. To pierwsza i najważniejsza weryfikacja poprawności wykonania prac. Podobnie, jeśli instalacja gazowa w budynku mieszkalnym lub użyteczności publicznej przechodzi gruntowną przebudowę lub poważny remont. Wymiana fragmentów rur, zmiana ich przebiegu, czy instalacja nowych przyłączy – każda z tych czynności narusza integralność systemu i wymaga ponownej weryfikacji szczelności. Pamiętajmy, gaz to nie powietrze, jego ulotność i łatwopalność sprawiają, że każdy, nawet najmniejszy przeciek, stanowi poważne zagrożenie.
Co więcej, prawo przewiduje scenariusz, w którym instalacja gazowa została wyłączona z użytkowania na okres dłuższy niż 6 miesięcy. Może to dotyczyć nieruchomości niezamieszkanych, obiektów sezonowych, lub sytuacji, gdy użytkownik zdecydował się na czasowe odłączenie gazu. Po upływie tego okresu, ponowne uruchomienie instalacji jest możliwe dopiero po przeprowadzeniu pozytywnej próby szczelności. To swoisty przegląd zerowy po "uśpieniu" systemu, mający na celu wykrycie potencjalnych uszkodzeń, które mogły powstać w czasie bezczynności, np. w wyniku korozji czy osiadania budynku. Zastanówmy się przez chwilę, co by było, gdybyśmy po pół roku nieużywania auta, ruszyli w daleką trasę bez sprawdzenia choćby ciśnienia w oponach? Podobnie jest z gazem.
Ostatnim, acz równie ważnym przypadkiem wymagającym ponownej próby szczelności, jest sytuacja, gdy nowa instalacja gazowa nie została napełniona gazem w okresie 6 miesięcy od daty przeprowadzenia pierwszej głównej próby szczelności. Wydawać by się mogło, że skoro raz test wypadł pomyślnie, to wystarczy. Jednak, w tym czasie, pomimo braku gazu pod ciśnieniem, system jest narażony na działanie czynników zewnętrznych, takich jak zmiany temperatury, wilgotności, a nawet mikroruchy strukturalne budynku. Pół roku to wystarczający czas, by pozornie szczelne połączenie stało się słabym punktem. Dlatego też, przed wpuszczeniem gazu do "nieaktywnego" systemu, konieczne jest ponowne badanie. To zapobiega niespodziankom i gwarantuje, że instalacja będzie gotowa na bezpieczną eksploatację. Te wszystkie sytuacje, choć z pozoru różne, łączy jeden cel: maksymalizacja bezpieczeństwa poprzez eliminację ryzyka wycieku gazu. Protokół z przeprowadzonej próby szczelności jest formalnym potwierdzeniem spełnienia tego celu.
Jak przebiega główna próba szczelności instalacji gazowej?
Przeprowadzenie głównej próby szczelności instalacji gazowej to precyzyjnie określony proces, który wymaga nie tylko specjalistycznego sprzętu, ale także odpowiednich kwalifikacji i obecności właściwych stron. Nie jest to zadanie dla domowego majsterkowicza, a dla profesjonalisty posiadającego stosowne uprawnienia budowlane do kierowania robotami budowlany w zakresie instalacji gazowych. Co więcej, zgodnie z przepisami, próba szczelności przeprowadza wykonawca instalacji w obecności dostawcy gazu. To trochę jak odbiór mieszkania od dewelopera – muszą być obecni zarówno wykonawca, jak i przedstawiciel "dostawcy" ostatecznego produktu, czyli w tym przypadku gazu. Ta procedura podwójnej kontroli ma na celu zapewnienie transparentności i obiektywności wyników.
Sama próba nie odbywa się w całym systemie jednocześnie, o ile mówimy o standardowej instalacji podłączonej do sieci gazowej. Próbę szczelności przeprowadza się odrębnie dla części instalacji przed gazomierzem oraz odrębnie dla pozostałej części z pominięciem gazomierzy. Dlaczego tak? Gazomierz to delikatne urządzenie pomiarowe, które mogłoby zostać uszkodzone przez ciśnienie próbne stosowane podczas głównej próby. Dodatkowo, fragment instalacji przed gazomierzem często leży w gestii dostawcy gazu, natomiast od gazomierza w głąb obiektu – w gestii właściciela. Rozdzielenie próby ułatwia identyfikację ewentualnych problemów i określenie zakresu odpowiedzialności za ich usunięcie.
Zanim jednak rozpocznie się pompowanie czynnika próbnego do rur, instalacja musi zostać odpowiednio przygotowana. Próbę szczelności przeprowadza się na instalacji nie posiadającej zabezpieczenia antykorozyjnego, po jej oczyszczeniu, zaślepieniu końcówek, otwarciu kurków i odłączeniu odbiorników gazu. Brak powłoki antykorozyjnej pozwala na wzrokową inspekcję wszystkich połączeń i spoin. Oczyszczenie rur z wszelkich pozostałości montażowych zapobiega zatykaniu delikatnych manometrów i innych urządzeń kontrolnych. Zaślepienie końcówek rur i odłączenie odbiorników gazu, takich jak piece czy kuchenki, jest oczywiste – system musi być zamknięty, a energia próbna nie może uciekać do atmosfery lub potencjalnie uszkodzić podłączonych urządzeń. Otwarte kurki wewnętrzne zapewniają, że cała objętość instalacji jest poddawana próbie, a nie tylko jej fragmenty między zaworami. Protokół z przeprowadzonej próby szczelności w obiekcie powinien szczegółowo opisywać sposób przygotowania instalacji do badania.
Jako czynnik próbny najczęściej stosuje się powietrze, rzadziej azot, ale nigdy gaz ziemny. Stosowanie gazu ziemnego do próby szczelności byłoby niezwykle niebezpieczne z uwagi na jego łatwopalność i możliwość stworzenia mieszaniny wybuchowej w przypadku nieszczelności. Po odpowiednim przygotowaniu i napełnieniu instalacji czynnikiem próbnym do odpowiedniego ciśnienia, następuje okres stabilizacji. Ciśnienie w instalacji może początkowo nieznacznie fluktuować w zależności od temperatury, co jest zjawiskiem normalnym. Dopiero po ustabilizowaniu się ciśnienia, rozpoczyna się właściwy czas próby, którego długość i minimalne ciśnienie próbne są ściśle określone przepisami. Każdy, kto przeprowadza taką próbę, doskonale wie, że chodzi o zero tolerancji na spadek ciśnienia – każdy, nawet najmniejszy, świadczy o nieszczelności, którą trzeba zlokalizować i usunąć. Ten proces, choć techniczny, ma ogromne znaczenie dla codziennego bezpieczeństwa. Można powiedzieć, że jest to test na "życie lub śmierć" dla instalacji gazowej, choć oczywiście nikt nie życzy sobie najgorszego.
Niezbędne narzędzia i wymagania dotyczące manometru
Skuteczna próba szczelności instalacji gazowej, jak każda precyzyjna procedura techniczna, wymaga użycia odpowiednich, skalibrowanych narzędzi pomiarowych. Królem wśród nich, w kontekście próby szczelności, jest bez wątpienia manometr. To on "opowiada" nam o ciśnieniu w systemie i o tym, czy to ciśnienie utrzymuje się na stałym poziomie, czy spada, sygnalizując potencjalne problemy. Jednak nie każdy manometr nadaje się do tego celu. Przepisy prawa są w tej kwestii niezwykle restrykcyjne i precyzyjne, a to z dobrego powodu. Precyzja pomiaru ma tutaj kluczowe znaczenie. Nawet minimalny spadek ciśnienia może wskazywać na niebezpieczny przeciek.
Zgodnie z wymogami, manometr użyty do przeprowadzenia głównej próby szczelności powinien spełniać wymagania klasy 0,6 i posiadać świadectwo legalizacji. Co to oznacza w praktyce? Klasa 0,6 świadczy o wysokiej dokładności pomiarowej manometru. Im niższa klasa, tym precyzyjniejszy jest przyrząd. W przypadku instalacji gazowych, gdzie stawką jest bezpieczeństwo, wymagana jest właśnie taka wysoka precyzja. Świadectwo legalizacji natomiast, to dokument potwierdzający, że manometr został poddany oficjalnym badaniom metrologicznym i spełnia normy w zakresie dokładności pomiaru. To jak paszport dla przyrządu, gwarantujący, że wskazywane przez niego wartości są rzetelne i zgodne ze stanem faktycznym. W protokole z próby szczelności bezwzględnie należy wpisać pełne dane użytego przyrządu pomiarowego, w tym jego numer seryjny i datę ważności legalizacji. To zapewnia identyfikowalność i odpowiedzialność.
Równie ważne jak klasa i legalizacja jest odpowiedni zakres pomiarowy manometru. Wybór właściwego zakresu zależy od ciśnienia próbnego, jakie będzie stosowane podczas badania. Ciśnienie czynnika próbnego w czasie przeprowadzania głównej próby szczelności powinno wynosić 0,05 M (co w przybliżeniu odpowiada 50 mbar). Dla takiego ciśnienia próbnego, zakres pomiarowy manometru powinien wynosić 0-0,06 M. Jest to rozsądny zakres, który zapewnia dokładne wskazania w pobliżu wymaganego ciśnienia próbnego, jednocześnie unikając sytuacji, w której skala byłaby zbyt "rozciągnięta", a odczyt niedokładny. Czasami jednak, w zależności od specyfiki instalacji, stosuje się wyższe ciśnienie próbne. Dla instalacji lub jej części znajdującej się w pomieszczeniu mieszkalnym lub w pomieszczeniu zagrożonym wybuchem, ciśnienie czynnika próbnego powinno wynosić 0,1 M (czyli około 100 mbar).
W przypadku wyższego ciśnienia próbnego, wynoszącego 0,1 M, zakres pomiarowy manometru powinien być odpowiednio większy, a mianowicie 0-0,16 M. Dobór manometru z zakresem nieco wyższym od stosowanego ciśnienia próbnego pozwala na bezpieczne i dokładne monitorowanie ciśnienia przez cały czas trwania próby. Zastosowanie manometru o zbyt małym zakresie mogłoby skutkować przekroczeniem maksymalnej wartości skali i potencjalnym uszkodzeniem przyrządu, a także uniemożliwiłoby właściwy pomiar. Natomiast manometr o zbyt dużym zakresie pomiarowym dla niskich ciśnień próbnych miałby zbyt "skompresowaną" skalę w interesującym nas przedziale, co utrudniałoby dokładny odczyt niewielkich spadków ciśnienia. Dlatego tak ważne jest precyzyjne dopasowanie manometru do parametrów próby. Te pozornie drobne detale techniczne są kluczowe dla rzetelności całego badania i bezpieczeństwa przyszłej eksploatacji instalacji. Właściwie dobrany i legalizowany manometr to niczym stetoskop dla lekarza – narzędzie pozwalające postawić właściwą diagnozę stanu instalacji. Można by rzec, że dobry manometr to połowa sukcesu w zapewnieniu szczelności, a tym samym bezpieczeństwa.
Ocena wyników próby szczelności i klasyfikacja przecieków
Punktem kulminacyjnym całej procedury jest ocena wyników przeprowadzonej próby szczelności instalacji gazowej. Po ustabilizowaniu się ciśnienia czynnika próbnego w systemie, rozpoczyna się właściwy czas obserwacji, który wynosi standardowo 30 minut. To właśnie w tym półgodzinnym oknie decyduje się, czy instalacja jest bezpieczna do dalszej eksploatacji, czy też wymaga dodatkowych prac i poprawek. Wynik głównej próby szczelności uznaje się za pozytywny, jeżeli w czasie tych 30 minut od ustabilizowania się ciśnienia czynnika próbnego nie nastąpi spadek ciśnienia. Nawet najmniejszy, zauważalny na precyzyjnym manometrze spadek ciśnienia jest sygnałem alarmowym, który oznacza, że instalacja jest nieszczelna i konieczne jest zlokalizowanie i usunięcie przyczyny tego stanu rzeczy. Prosto mówiąc, albo ciśnienie stoi w miejscu jak zaczarowane, albo coś jest nie tak. To jest ten moment prawdy.
Zrozumienie skali problemu i priorytetu działań naprawczych ułatwiają normy, które klasyfikują przecieki gazu na różne kategorie. Jedną z powszechnie stosowanych klasyfikacji, choć w Polsce bazujemy przede wszystkim na własnych przepisach, są wytyczne niemieckich DVGW-TRGI. Rozróżnia się 3 stopnie szczelności w zależności od zamierzonej wielkości przecieków gazu. To bardzo praktyczne podejście, bo nie każdy przeciek wymaga natychmiastowej paniki. Pierwszy stopień to szczelność pełna, charakteryzująca się przeciekami poniżej 1 l/h. Przewody gazowe w takim przypadku można eksploatować bez obaw. Instalacja jest w idealnym stanie. To jakby auto, które przeszło przegląd bez żadnych uwag – możesz spokojnie wsiadać i jechać w najdłuższą podróż.
Drugi stopień to szczelność obniżona, dotycząca przecieków w przedziale 1,0-5,0 l/h. W takim przypadku instalacja nie jest w pełni szczelna, ale ryzyko związane z tak niewielkim przeciekiem nie wymaga natychmiastowego wyłączenia systemu z eksploatacji. Należy jednak podjąć działania, aby przywrócić pełną szczelność w ciągu 4 tygodni. To jakby lekarz zalecił wizytę kontrolną za miesiąc w związku z niewielkim, ale zauważonym problemem. Jest czas na spokojne zaplanowanie napraw, ale nie można o nich zapomnieć. Taki stan wymaga interwencji, ale nie stwarza bezpośredniego zagrożenia, o ile sytuacja jest pod kontrolą i w określonym czasie zostaną przeprowadzone odpowiednie prace.
Najbardziej alarmującą kategorią są przewody nieszczelne, charakteryzujące się przeciekami powyżej 5 l/h. Taki poziom przecieku świadczy o poważnym problemie z integralnością instalacji gazowej i stanowi bezpośrednie zagrożenie dla życia i zdrowia. Przewody nieszczelne wymagają natychmiastowego wyłączenia z eksploatacji. Nie ma tutaj mowy o odkładaniu problemu na później. Gaz ulatniający się w takiej ilości w zamkniętych przestrzeniach może bardzo szybko stworzyć mieszaninę wybuchową lub doprowadzić do zatrucia. To jak czerwona lampka ostrzegawcza w kokpicie samolotu – sygnalizuje krytyczną awarię, która wymaga natychmiastowej reakcji i przerwania "lotu". Protokół z przeprowadzonej próby szczelności w obiekcie powinien jasno wskazywać na stopień szczelności instalacji.
Ocena wyników próby szczelności to nie tylko odczyt z manometru. Proces ten obejmuje również szereg dodatkowych sprawdzeń, mających na celu kompleksową weryfikację stanu instalacji. Doświadczony specjalista sprawdzi zgodność ułożenia przewodów gazowych z projektem. Odstępstwa od projektu mogą świadczyć o potencjalnych problemach montażowych lub o braku wymaganych przepisami odstępów bezpieczeństwa od innych instalacji. Sprawdza się również zgodność ułożenia rur spalinowych z projektem – właściwe odprowadzanie spalin jest równie kluczowe dla bezpieczeństwa co szczelność instalacji gazowej. Kontroli podlegają również materiały użyte do budowy instalacji gazu, czy są zgodne z projektem i obowiązującymi normami. Na koniec, a może przede wszystkim, dokładnie sprawdza się jakość połączeń – skręcanych, spawanych i zaprasowywanych. To właśnie na połączeniach najczęściej pojawiają się nieszczelności. Starannie wykonana spoina czy połączenie zaprasowywane to fundament szczelnej instalacji. Wszystkie te punkty kontrolne sumują się na rzetelną ocenę stanu instalacji i pozwalają na sporządzenie kompleksowego protokołu, będącego świadectwem bezpieczeństwa lub listą usterek do naprawienia. To trochę jak policyjne dochodzenie po zdarzeniu – zbiera się wszystkie poszlaki, analizuje fakty, aby wydać ostateczny werdykt dotyczący "winy", czyli w tym przypadku nieszczelności i jej skali.
Q&A
Czym jest protokół z przeprowadzonej próby szczelności instalacji gazowej w obiekcie?
To dokument potwierdzający, że instalacja gazowa przeszła pozytywną próbę szczelności, co jest wymagane prawem i świadczy o jej bezpieczeństwie.
Kiedy trzeba wykonać próbę szczelności instalacji gazowej?
Próba jest wymagana przy nowych instalacjach, po przebudowie lub remoncie, po wyłączeniu z użytkowania na dłużej niż 6 miesięcy oraz gdy nowa instalacja nie została napełniona gazem przez 6 miesięcy od poprzedniej próby.
Kto przeprowadza próbę szczelności i kto musi być obecny?
Próbę przeprowadza wykonawca instalacji z odpowiednimi uprawnieniami w obecności dostawcy gazu.
Jaki manometr jest wymagany do próby szczelności?
Wymagany jest manometr klasy 0,6 ze świadectwem legalizacji, z odpowiednim zakresem pomiarowym dostosowanym do ciśnienia próbnego (np. 0-0,06 M dla 0,05 M ciśnienia próbnego).
Jak ocenia się wynik próby szczelności instalacji gazowej?
Wynik jest pozytywny, jeśli przez 30 minut po ustabilizowaniu się ciśnienia próbnego nie nastąpi spadek ciśnienia. Klasyfikuje się również stopnie szczelności na podstawie wielkości przecieków.